製造業の「DX」って何だろう?
製造現場の声
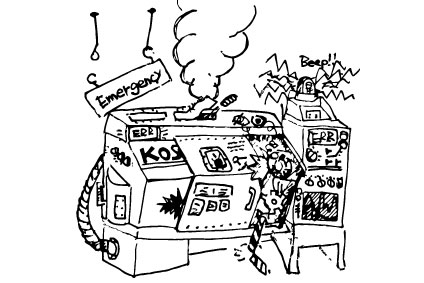
最近、テレビでもネットでも雑誌でも、「DX」(*1)や「IoT」(*2)の話題は欠かさないし、
大手製造企業が我さきに導入しようとしているというニュースがでてますが、製造業の現場の方からは、
実施目的や投資対効果が見えないので、世間で騒いでいるほど、経営陣も本気でやらなければならないと
思ってはいない。という話をよく聞きます。今一度、製造現場の視点から何のための「DX」なんだろうと考えてみました。
例えば、こんな会話があったとします。
製造課長
「先月の第2加工ラインの生産数が落ちているけど、何かあったの?」
ラインの責任者
「そうなんですよ、月初めに加工機の調子が悪くて、メンテナンスをしたけど、何回か加工機が止まっちゃったんです。
でも、生産技術の〇〇係長に調整してもらったら調子が良くなって、後半、残業したから、かなり持ち直したんですけど。」
製造課長
「なるほど、それはよかった。それなら、問題なさそうだね。」
実は、この会話の裏に隠されている事実がある。
・実は、以前から加工機の調子が悪い状態が続いていた。
・空調機が故障してて、室温が高かった。
・先月末からこの加工機の稼働率が高くなっていた。
・来月もこの加工機の稼働率が高くなるはず。
・加工機の定期メンテナンスがされてない。
・抜本的な故障対応をしていないので、再度、加工機が停止する可能性が高い。
・機械が古いので、〇〇係長がいないと、復旧(調整)できない。
それで、どうなったかというと・・・
月半ばになって、加工機が突然停止してしまう。〇〇係長は海外出張中、来週帰国の予定で捕まらない。
メーカーに連絡したが、古い機械なので、交換部品の在庫がなく、修理は、来週以降になるということ。
納期が間に合わなくなるかもしれないが、どこまで影響があるかわからない。
客観的事実と因果関係
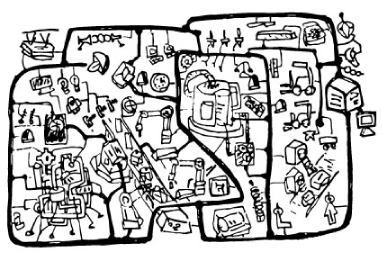
もしも、客観的に状況が把握できればどうなっていたでしょうか?
・機器の不調の前兆
・機器の稼働状況
・機器の停止、ライン停止の客観的事実
・環境情報(機器の温度、室温など)
・消耗工具やメンテナンス部品の交換時期
・機器の耐久年数
・保守、メンテナンス情報
・生産計画と実績
・工員の状態
これらの情報があれば、客観的な判断ができ、万が一の場合のライン停止の影響や予測ができたかもしれない・・・
現場ではあたりまえの事実であっても、個々の情報が、総合的に、客観的な事実として見れるかどうか?
問題を発見できても、その他の事象との要因の関係性を見つけ出せるのだろうか?
昔は、
・機器の音を聞くだけで、不調の箇所がわかる。
・気温の変化を肌で感じて、メンテナンスをする。
・触ってみて、軸のブレを調整する。
・見ただけで、刃具の取り換え時期がわかる。
・「こいつとは、長い付き合いだからな・・・」と言って、故障を直してしまう。
・それでもだめなら、最後は、社員を総動員してでも、納期に間に合わせてしまう。
っていう、匠のおやじさんがいっぱいいた。
それが、IoTを使って
・機器の不調の前兆がとらえられて
・機器の稼働状況が見えて
・機器の停止、ライン停止の客観的事実がわかって
・環境情報(機器の温度、室温など)がとれて
・消耗工具やメンテナンス部品の交換時期がわかって
・機器の耐久年数や過去の保守、メンテナンス情報が確認でき
・生産計画と実績や工員の状態がわかる。
仕組みができれば、
客観的事実を把握することができ、それぞれの事象の因果関係が見える。
そして、万が一の場合のライン停止や不良の影響や予測ができれば、客観的な判断を早い段階ですることができるはずで、予防処置もできたかもしれない。
そのためには、
ラインの実績情報から、設備の状態や環境との因果関係も併せて、販売管理や生産管理情報の需要情報、計画情報、生産実績、出荷情報、在庫や調達情報、
全ての工場の状態を把握する。
そして、AIが工場で起きている様々な事象から問題を発見できる。
そんな未来が見えてきます。
IoT品質
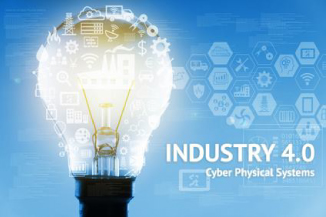
それでは、製造現場のDXは、本当に必要なのか?現場視点からもう少し視点を上げて考えてみましょう。
例えば、見込・大量生産の企業であれば、設備の故障が大きな影響を及ぼすし、それぞれのリードタイムが、ほんの少しでも
縮まれば、大きな効果があるし、それぞれのコストが、ほんの少しでも下がれば、大きな利益になるので、IoTを導入する意味って
案外大きいのかもしれない。
それじゃあ受注生産の多品種小量生産の企業ならどうなんだろう?そういう企業がIoT導入に踏み切れ
ないのは、IoTの導入コストに対して、リードタイム短縮やコスト削減では、採算が取れないから?効果が図れないから?やっぱり、
そういう企業の経営陣が「DX」の看板を挙げて、やれ「リードタイム短縮だ」「コスト削減だ」って言っているうちは、いつまで
経っても決心できないような気がします。
ここで、やっぱり、必要なキーワードは、「品質の軸」
でも、品質を上げるために、初期導入コストやランニングコストを払ってまで、IoTを導入しないといけない理由がどこにあるんだろうか?
最近、利益重視で、コスト、スピード、量を優先するあまり、「質よりスピード」「質より量」「質よりコスト」っていう傾向が多く、
世間をお騒がせする企業も多いですが、それでは、企業が生き残っていけるはずがありません。この先、「IoT」を導入しているからこそ
将来に渡って、安定的なコストで需要にあった製品を適時供給でき、安全、安心を保証する品質と環境への配慮ができる。
そういった付加価値を担保するために「IoT品質」を要求される日が来るはずです。
情報基盤
しかしながら、IoTの導入の前にやっておかないといけないことがあります。
それは、「情報基盤整備」
IoTって、「もののインターネット」つまり、その「もの」の環境、動き、位置、状態を検知し、インターネットで情報を収集する
ことで、センサーと通信機器とネットワークやインフラの事を言っている場合が多いです。この辺りは、私、本業ではないので、
専門家におまかせしたいところですが、ものの情報を収集するだけだと、あまり意味がありません。
例えば、設備の情報を集めたらその設備の稼働状況や状態がわかるかもしれません。でも、あくまで、それ単体の設備の情報が
リアルタイムに見えたり、分析することができるようになるかもしれませんが、所詮、それだけの事でしかない。
色々な情報を相互につなげて見えるようにすることに意味があるのであって、単体で情報があっても、せっかく集めた情報が粗大ごみ化して
しまいます。そして、設備の稼働状況、ラインの加工や組立の状況、部材の情報、それから生産計画や生産実績情報や設計情報
とつながっている必要があります。
設備の稼働状況であれば、その設備の環境、動き、位置、状態だけじゃなく、「どのオーダーの」「どの製品の」「どの部品の」
だとか、「どの工程の」「どのロットの」「誰の担当の」などのキー情報が関連づいている。つまり、設備の稼働状況の情報に、
製品番号、オーダー番号、品目番号、工程番号、ロット番号、担当者番号が関連づいているっていうことです。
そうすることで、ひとつの情報では見えなかったものが、お互いの情報があるから相関関係が見えるし、複合的な要素が見えてくるからこそ、どこ
に問題があるかが見えてくる。
例えば、
生産計画情報からオーダー、オーダーから製品、部品表の構成情報をたどって、品目や工程、そして、設備情報や設備の稼働状況
を見ることができる。設備の稼働状況から工程や品目、部品表の構成情報をたどって製品の情報や注文や出荷情報をみることができる。
そういう、設計情報(部品表)、販売管理情報、生産管理情報、製造情報に加えて、設備の稼働状況のようなビックデータにキー(ID)
情報を関連付けて、抽出、連携、分析がリアルタイムにできる仕組みが情報基盤なんです。
だから、製造現場のビッグデータをクラウド環境に集めて、分析をしても、何の意味もありません。製造現場のビッグデータをどう
関連付けて見せるか(分析するのか?)っていう要件を先に想定しておかないと、高額なごみデータ収集マシンと、高額なゴミ箱に
なってしまいかねません。
製造現場の「DX」
つまり、製造現場の「DX」は、IoTで製造現場の設備、機器、環境、ライン稼働状況などをつないで、見える化することだけじゃなくて、
「変動要素をシミュレーションできること」
「それらをいかにコントロールできるか」
という要件とつなげることが、本来の製造現場の「DX」の目的になるべきです。
では、もう少し具体的に話をしてみましょう。
現在の状況がわかる(見える)ことは大前提として、過去と現在と未来の時間軸の状況がわかる(見える化)必要があります。
つまり、過去にさかのぼって、状況の分析ができる。これは、実績情報を収集していれば、おのずとできることなんですが、
未来を予測することは、現在の状況からいくつかの要素でシミュレーションをしないとできません。
それには、「需要予測→販売計画→生産計画→受注→製造オーダー→手配→加工→組立→検査→出荷」のSCM軸の一連の情報が
つながっていないといけません。そして、「製品→設計部品表→生産部品表」の新商品設計軸とSCM軸との接点がちゃんとつながってて、
最後に製造に必要なリソースとの関係をどうつなげることができるかどうかです。
製造に必要なリソースっていうのは、原材料や部品や中間品、製品などの在庫情報(品目と数量、保管場所や状態)、そして、人、
設備の情報や金型、治工具など、これらの状態や稼働状況の実績情報を収集し、リソースマスターに定義されたキャパシティや変動要素を
加味して、需要の変化にどう追従することができるかをシミュレーションする事ができる。
需要の変化により、将来、追加で必要になるリソースが何で、どの事業リスクを許容するのか?という経営判断できる材料(情報)が
導き出せるかどうかです。
いつかきっと
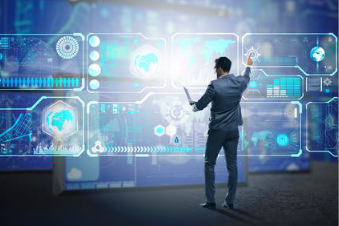
『VRゴーグルとサイバーグローブを付けた管理者が、3D表示された工場レイアウト上に表示されている。稼働状況を監視しながら、トラブルや
不具合発生時には、その状況や影響の予測を表示したり、対応策が提示される。
また、需要情報を投入すると、計画シミュレーションが行われ、ボトルネックになるラインや不足するリソースの警告が表示されたり、必要と
なるリソースや部材が明示され、承認をすると、即座に、ライン変更や手配変更指示がかかる。』そういう世界が実現できる日も、それほど、
遠くないかもしれません。
※本文で使用している「DX」と「IoT」は、以下の解釈で用いています。
*1)DX:(Digital transformation);情報技術と現実を融合して変化を起こすための枠組みや概念
*2)IoT(Internet of Things) :モノのインターネット 製造現場の設備、機器、環境、ライン稼働状況などをつないで、情報収集するための仕組み