BOPの話、始めました。
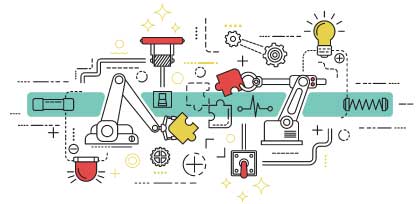
最近、多くのお客様先で、「BOP(Bill of Process)」というキーワードをお聞きします。
BOPは、BOM (Bill of Material)から派生した製造プロセスのマスタで、製品の姿を製造プロセスとリソースで構成されます。
BOP導入の目的はそれぞれありますが、製品ライフサイクルの量産立ち上げまでの期間短縮、グローバル生産における生産移管立ち上げ期間短縮、
製造実績や品質情報の設計へのフィードバックによる製品品質の向上、生産工程や設備の治具の準備などの有効利用、
特殊な生産条件の検知や品質の担保、生産基準や手順書の自動生成など、多くの効果が期待されています。
BOPって何?
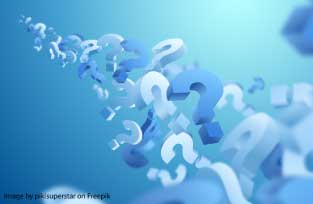
BOPとは、「Bill Of Process」の略で、「工程表」「工程マスタ」などと呼ばれることがあります。
これは、部品の加工や製品の組み立てのプロセスフローであり、製造品質を担保するための製造工程マスタともいえます。
例えば、工程情報のライン、工程、工順、検査、段取、それに、製造工程に必要な設備や治具、製造条件、標準類、
基準時間、製造図面などの製造関連情報も含まれます。また、これら「工程表」「工程マスタ」の情報は、
製品の品目構成に紐づいており、製品から品目構成、工程、工程に関連づいた製造関連情報までをたどることができます。
BOPの目的って何?
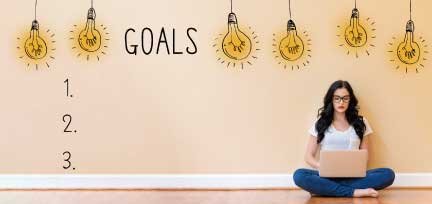
つまり、設計BOMから製造BOMへ製品構成情報を連携し、工程展開、生産準備プロセス全般にわたる情報の紐づきを行い、 製品構成と工程情報に製造情報を関連付けることで、製造にかかわるリソースを一元的に管理し、変更情報をERP、 MESや現場ラインのシステムへの自動連係したり、マスタ化された工程情報やリソース情報を流用することで、 新商品の量産立ち上げや生産移管の立ち上げのL/Tを短縮することもできます。 そして、ERP、MESのシステムや現場のIOTシステムの実績をBOPに集約することで、製造のQCDの見える化、 製造工程への改善につなげることができ、設計・開発プロセスとの情報共有や製造の実績情報をフィードバックすることで、 商品開発期間の短縮や製品コストダウンを図ることも可能になります。
BOP導入のメリット
では、BOP導入で想定される目的やメリットを、もう一度整理しておきましょう。
①新商品の立ち上げ際に、既存のBOP情報を流用したり、変化点を確認することができ、量産立ち上げまでの工数や時間を短縮することができる。
②生産移管を行う際に、移管元のBOPを流用したり、BOP情報の比較、製造の変化点を確認することができ、量産立ち上げまでの労力や時間を短縮することができる。
③設計変更(製造変更)の際に、製造工程における影響調査を行う事ができる。また、BOPを適用の起点にすることで、変更の適用管理を確実に行う事ができる。
④BOPの製品構成や工程関連情報からERP、MESや現場ラインのシステムへ情報を反映することができる。
⑤BOPの製品構成や工程関連情報に、ERP、MESや現場ラインのシステムの実績情報を集約することで、製造ラインの見える化や評価・分析、改善を行う事ができる。
⑥BOPの実績情報や品質情報を設計・開発プロセスへフィードバックすることで、設計品質の向上、商品開発期間の短縮やコストダウンを図ることができる。
BOP導入が進まない理由
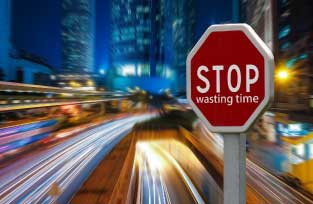
それでは、BOPの導入効果にこれだけのメリットがあるのに、なぜこれまで、BOPが浸透してこなかったのでしょうか?
実を言うと、10数年以上も前からBOPの概念があり注目されていましたが、生産工程やリソースのマスタの管理の
難易度が高く、変更の柔軟性に対応することが困難で、BOPのマスタを作成管理するだけのメリットが見いだせないでいました。
また、「製造プロセス全体を俯瞰して統括管理する部署がなく、各部署の管理業務プロセス毎に情報が分断されてしまっている。」
という事も大きな阻害要因でした。そして「BOMのストラクチャー構成に直接BOPのプロセスを関連付けることが難しい。」つまり、
BOMとBOPの関係には、ストラクチャー型でない構造(関係)を持つ仕組みが必要になります。
これらの仕組みは、「マトリックス部品表」だとか「スーパーBOM」だとか呼ばれることもありますが、自社の構成(関係)の在り方を
導き出し、これらの構造や仕組みを理解して、情報を登録・維持管理するのは、中々、ハードルが高いことになります。
また、「E-BOM(Engineering Bill of Material)、M-BOM(Manufacturing Bill of Material)の連携の問題が解決しないと、
設計プロセスから一気通貫で、BOP導入効果を得ることが難しい。」という事もあります。
どこに効果を求めるのか?
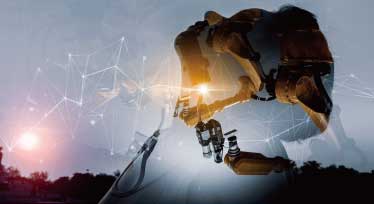
BOPを導入するには、PLMシステムの再構築が前提になり、ERPやMESのシステムとの連動も必要であり、大規模なシステム投資が 必要になります。また、BOPを維持・運営するための新しい組織が必要になるため、人的リソースも必要になります。 一方、BOP導入の効果を、設計プロセスや製造プロセスのコスト削減効果だけで測るのは難しく、BOP導入の投資を回収するには 全く及びません。BOP導入は、直接的なコスト削減効果よりも、「事業環境の変化の対応」と「多様なリスクの対応」の観点での 効果を測るべきで、グローバル戦略の要となる、新商品の投入スピード、新生産拠点の早期立ち上げ、生産移管の加速、そして、 増々、複雑化する仕様や生産条件に対応するための製造プロセスのDX化の基盤として位置づけるべきで、自然災害、戦争などに よる生産拠点の変更や調達問題の対応などのリスクにも追従していかねばならず、メガリコール対策のための設計・製造品質の 担保や影響を最小限にとどめるための将来のリスク投資としてもとらえる必要があるのではないでしょうか。
どこからやるべきか?
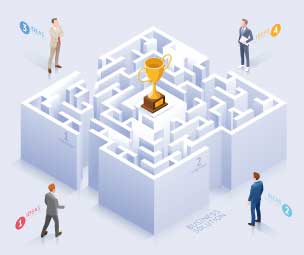
大きな投資に耐えられる大企業やダイナミックに改革を行う意思がある経営陣がいれば、上位の設計プロセスのPLMから一気通貫で
システムの導入ができるかも知れませんが、そうでないなら、まずは、ものつくりの現場の標準化を進めながら、製造ラインや工程
のリソース(設備や治具、製造条件、標準類、基準時間、製造図面)を一元管理し、製品や部品の情報と関連づけるためのマスタDB
を構築すること、そして、工程表をマスタ化し、M-BOMの製品や部品と関連付けることを目標とし、達成できた結果をもとに、上流か
らBOPという仕組みを導入し、最終形に持って行く。こうするのは、もう一つ理由があって、上流から導入した場合、部門を横断した
役割の新しい組織の立ち上げやマスタ化に多くの労力と時間がかかるため、運用が定着し本当の意味での導入効果がでるまで5年、
10年とかかる可能性があります。まずは、ものつくりの現場の標準化を起点に、下流から製造で必要な環境を整備し、効果を出しな
がらゴールを目指した方が、結果的に早く投資の回収を始めることができ、効果を見ながら次の投資の判断がすることができるはずです。
段階的にステップアップしていくシナリオ
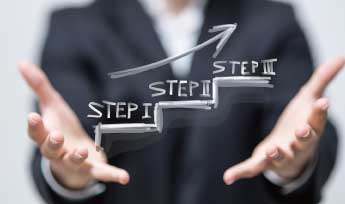
これまで、我々も多くのお客様で、BOPの話をお聞きしていますが、投資対効果を見極められず決心できなかったり、新しい組織や
役割の意義を説得できず断念したケースも多く、パッケージを導入すれば、効果が得られるとは考えない方がよさそうです。
それに、パッケージ自体も発展途上で、PLMのオプション機能であったり、生産管理のマスタ管理機能でしかない場合があり、本来の
BOPの概念を実現できる機能ではないパッケージも多いようです。
BOPのパッケージを導入したけど、多くのマスタを登録しないと動かないし、操作が複雑で融通が利かなくて、結局、使わない(使えない)
システムになってしまった。という事は避けなければなりません。
我々は、パッケージ先行で導入を進めるのではなく、ゴール設定をした上で、自分たちの実力に合わせて、ものつくりの現場の標準化を
起点に、効果がでることろから納得しながら段階的にステップアップしていくシナリオが必要だと考えます。